EI&C installation project
Pharmaceutical company in Basel
As one of the leading specialists in industrial automation of process plants, Penta-Electric has comprehensive experience in a wide range of industries – in Switzerland as well as abroad. This includes work for the pharmaceutical industry in particular. We’ll gladly accept any challenge head-on with our extensive expertise and experience, and prove to you that perfection is achievable.
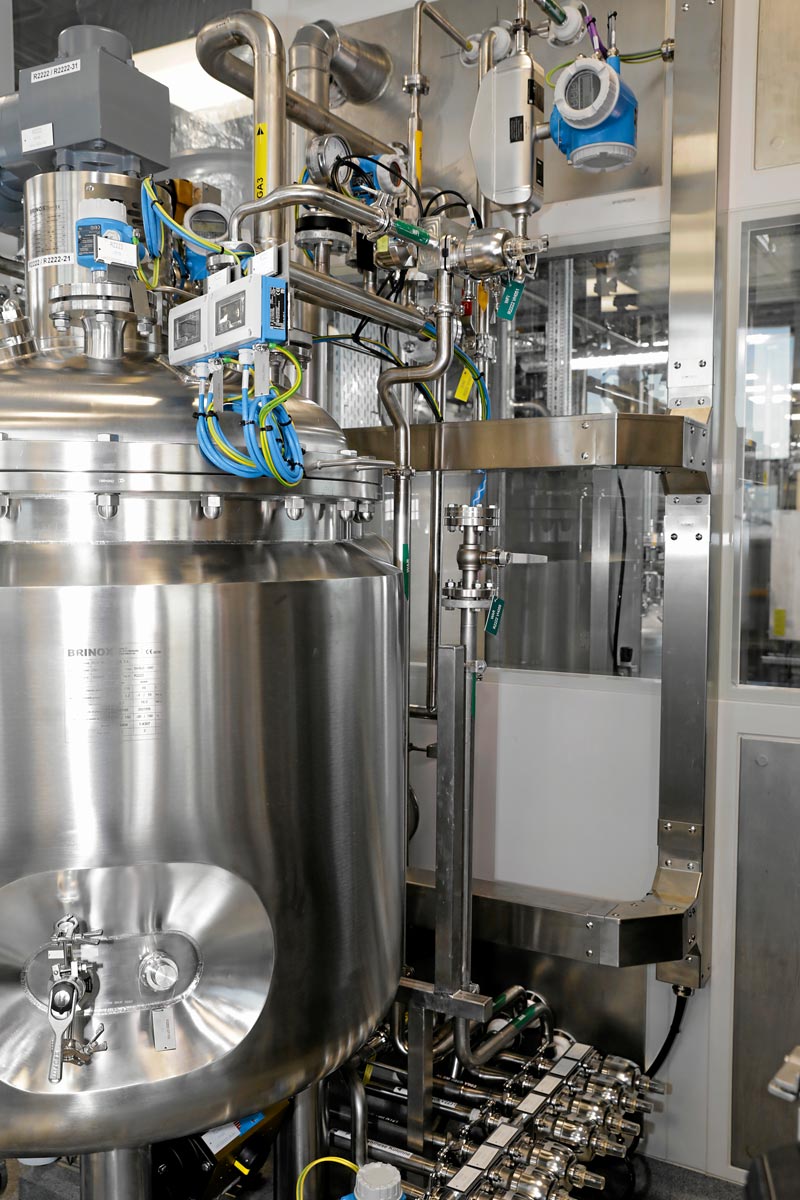
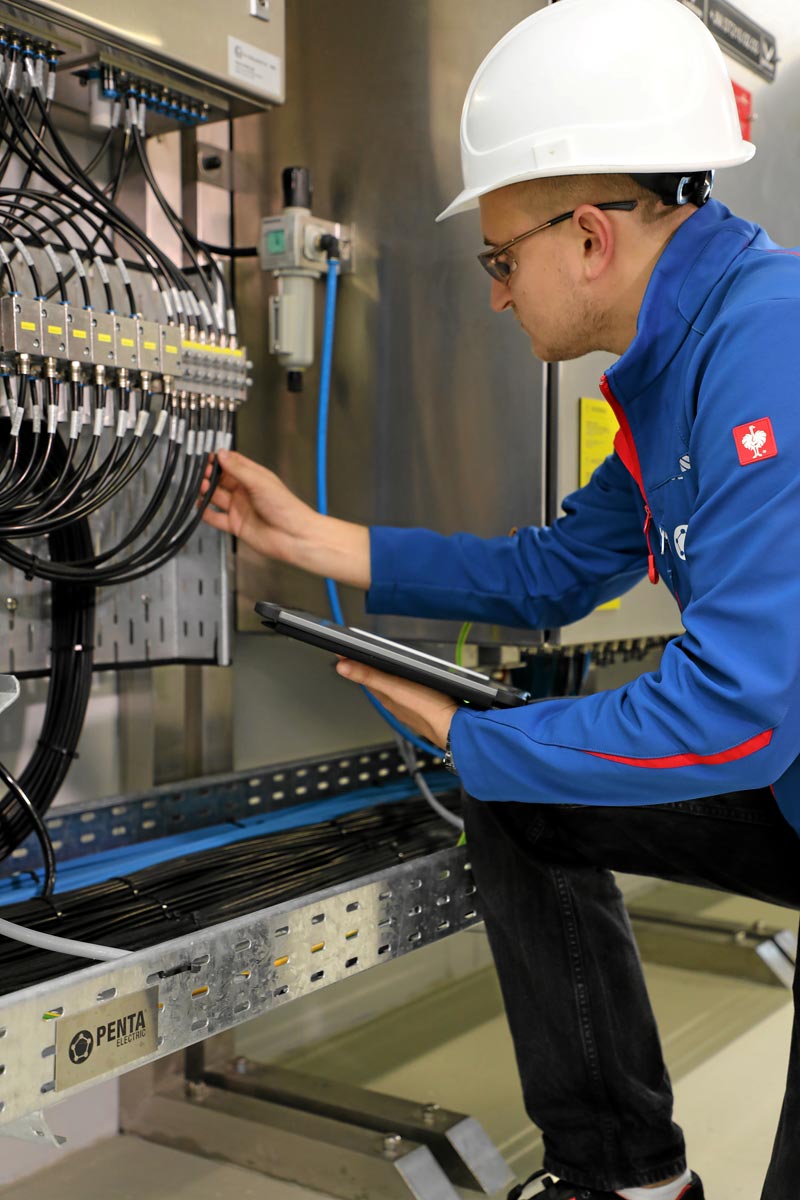
Project description:
A pharmaceutical company in Basel has constructed a new GMP-compliant API production plant in an existing building with complex technical requirements and strict schedules. New ventilation systems, clean rooms in various categories, plant areas for peripheral systems, as well as remote controls had to be installed in this building. A monitoring system for room data was also required. The cleanrooms have explosive zones and had to be installed in accordance with ATEX guidelines.
The requirements specified by the clients:
EI&C installations for the complete process automation and associated infrastructure
Cleanroom installations satisfying GMP requirements for categories C and D and ATEX
Support for line testing and installation qualification (IQ)
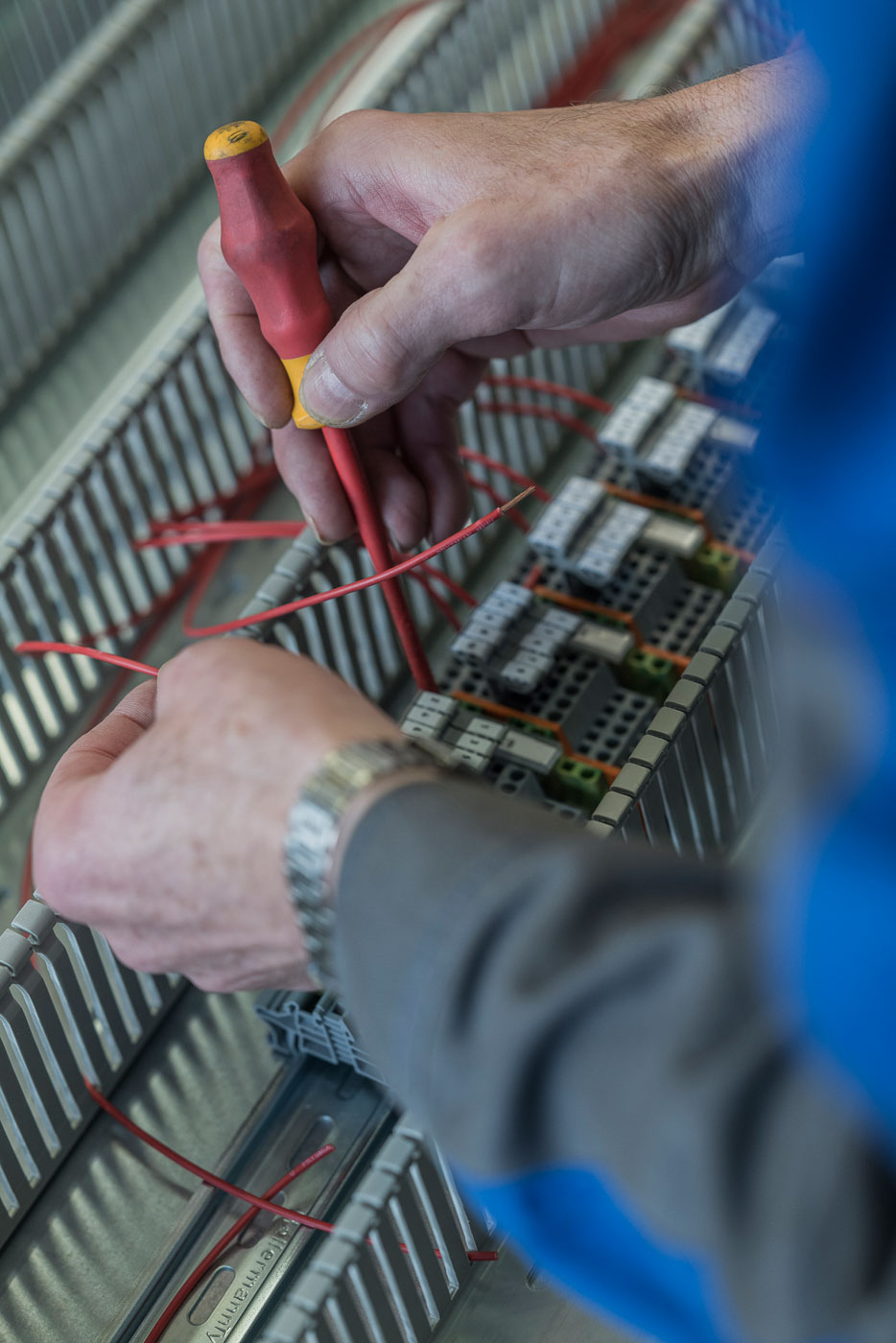
The custom-tailored solution from Penta-Electric:
Its experienced installation team enabled Penta-Electric to complete the installation while the planning phase was still in progress. Thanks to the specialist expertise and the commitment of our team, a high-quality solution delivered on time was guaranteed.
The benefits for the clients:
Our many years of experience with EI&C installation projects in the pharmaceutical, chemical and biotech industries form the foundation that enables Penta-Electric to develop targeted solutions even in critical situations and under time pressure. The comprehensive trust on both sides meant that the decision-making processes were short, which was crucial to the project’s success.
The challenge for Penta-Electric:
Solution-oriented collaboration between the project teams for a time-critical project during a global pandemic with all its implications, including supply difficulties, staff shortages and official measures.
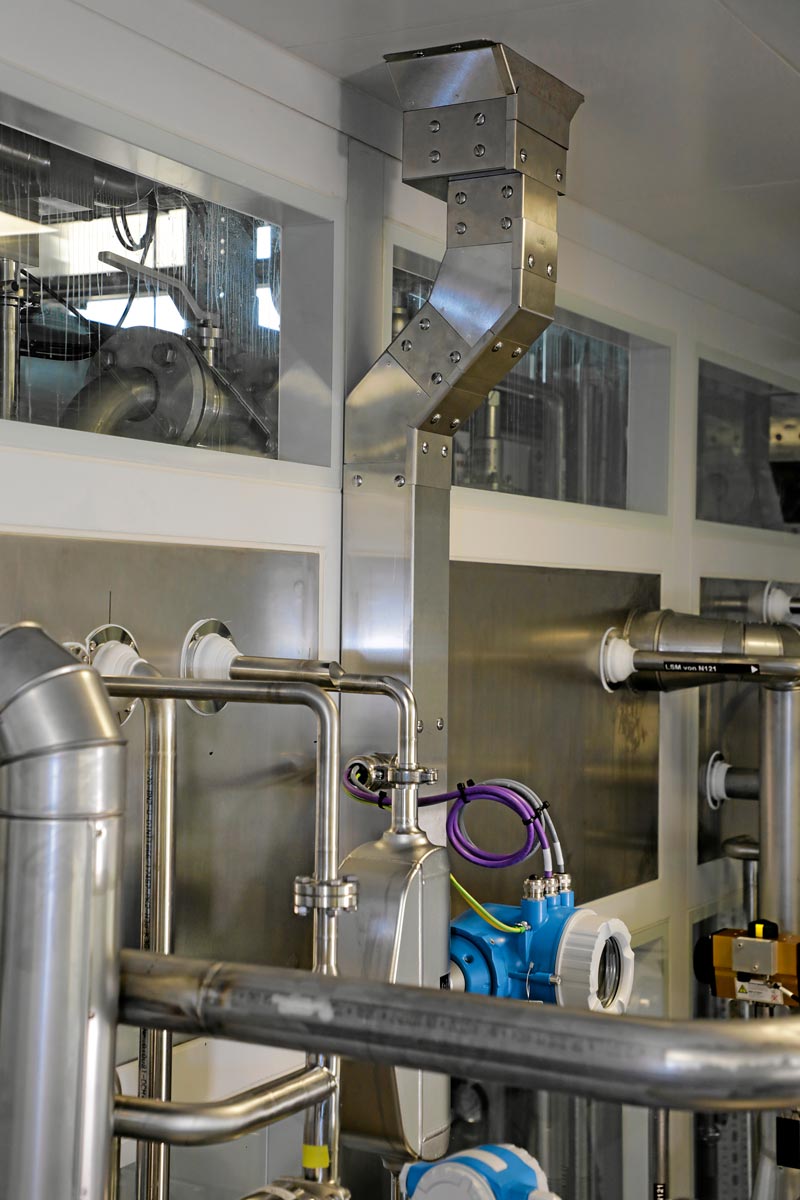
The project in figures:
Automation project
Automation of Oligo Building G for Bachem AG in Bubendorf
As one of the leading specialists in industrial automation of process plants, Penta-Electric has comprehensive experience in a wide range of industries – in Switzerland as well as abroad. This includes work for the pharmaceutical industry in particular. We’ll gladly accept any challenge head-on with our extensive expertise and experience, and prove to you that perfection is achievable.
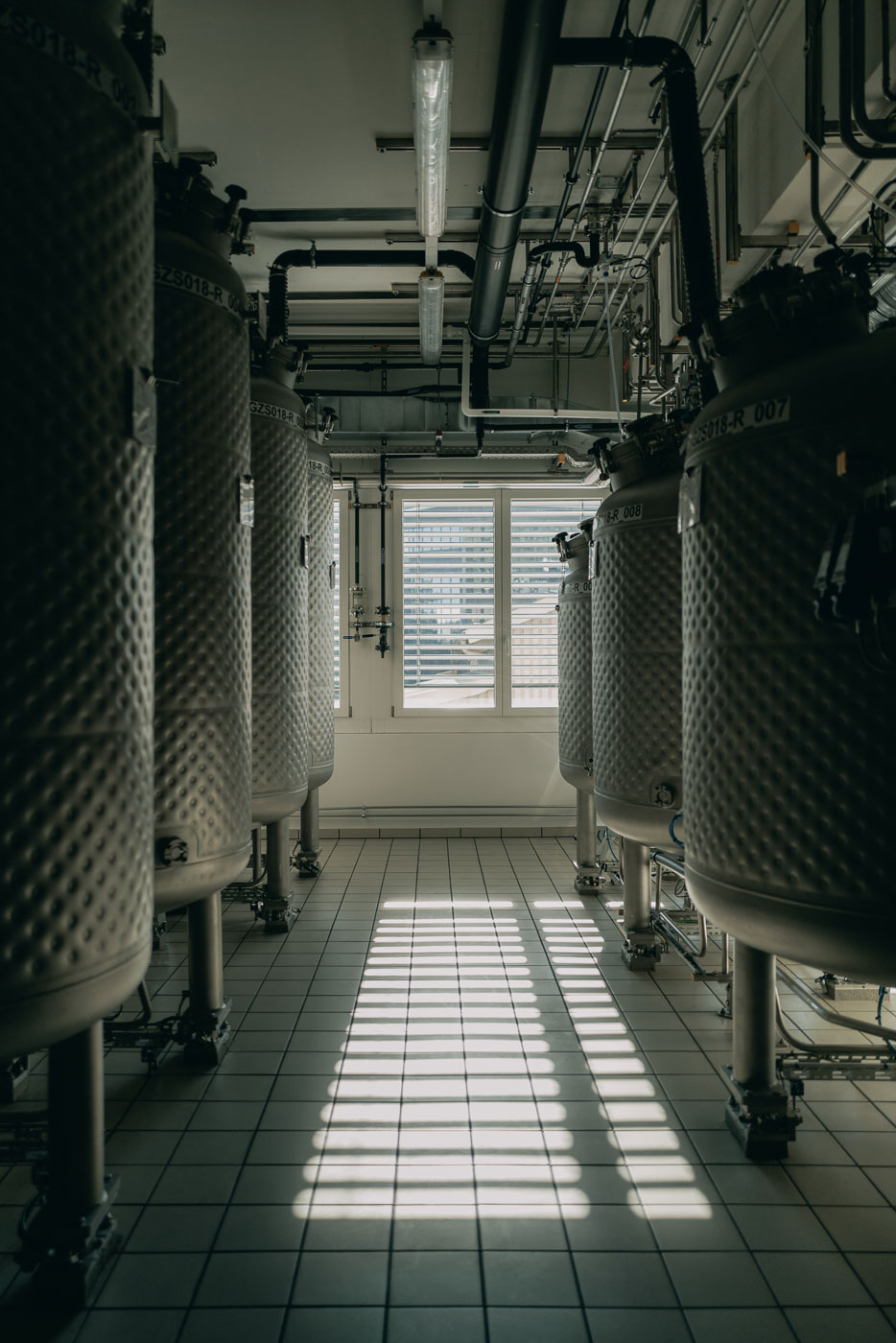
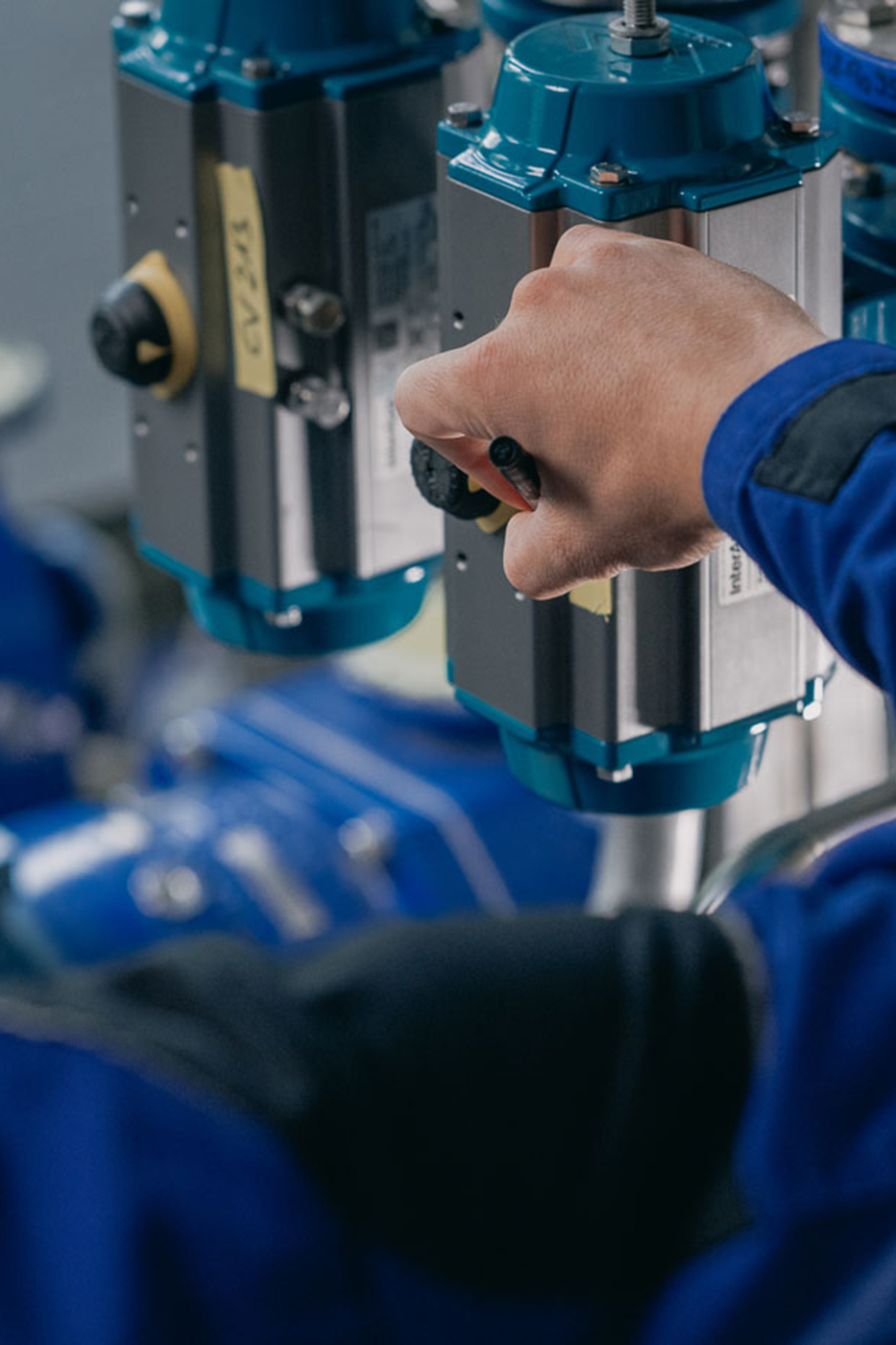
Project description
Bachem AG in Bubendorf constructed a new plant for producing oligonucleotides. The new process technology required an extended basic engineering phase.
This optimum preparatory work paved the way for quick execution of detailed engineering and project implementation and ensured that the completion deadline was met.
The requirements specified by Bachem AG
Engineering, supply and installation for the Oligo Building G project, with 6 mixed feeder systems (25 buffer tanks), 9 media panels, and connection to 8 package units:
- Hardware planning of the complete EI&C system
- Generating the good automated manufacturing practice (GAMP) documents and test documentation
- Programming the S7-1500 Control System and Zenon visualization with batch control
- Defining and implementing all interfacing with the package units
- Linking to the OSIsoft PI data historian system
- Factory acceptance testing (FAT) of all software to be used
- Supplying the automation components and switchgear cabinets
- Performing the on-site plant EI&C installation work
- Line testing and installation qualification
- Functional testing and operational qualification
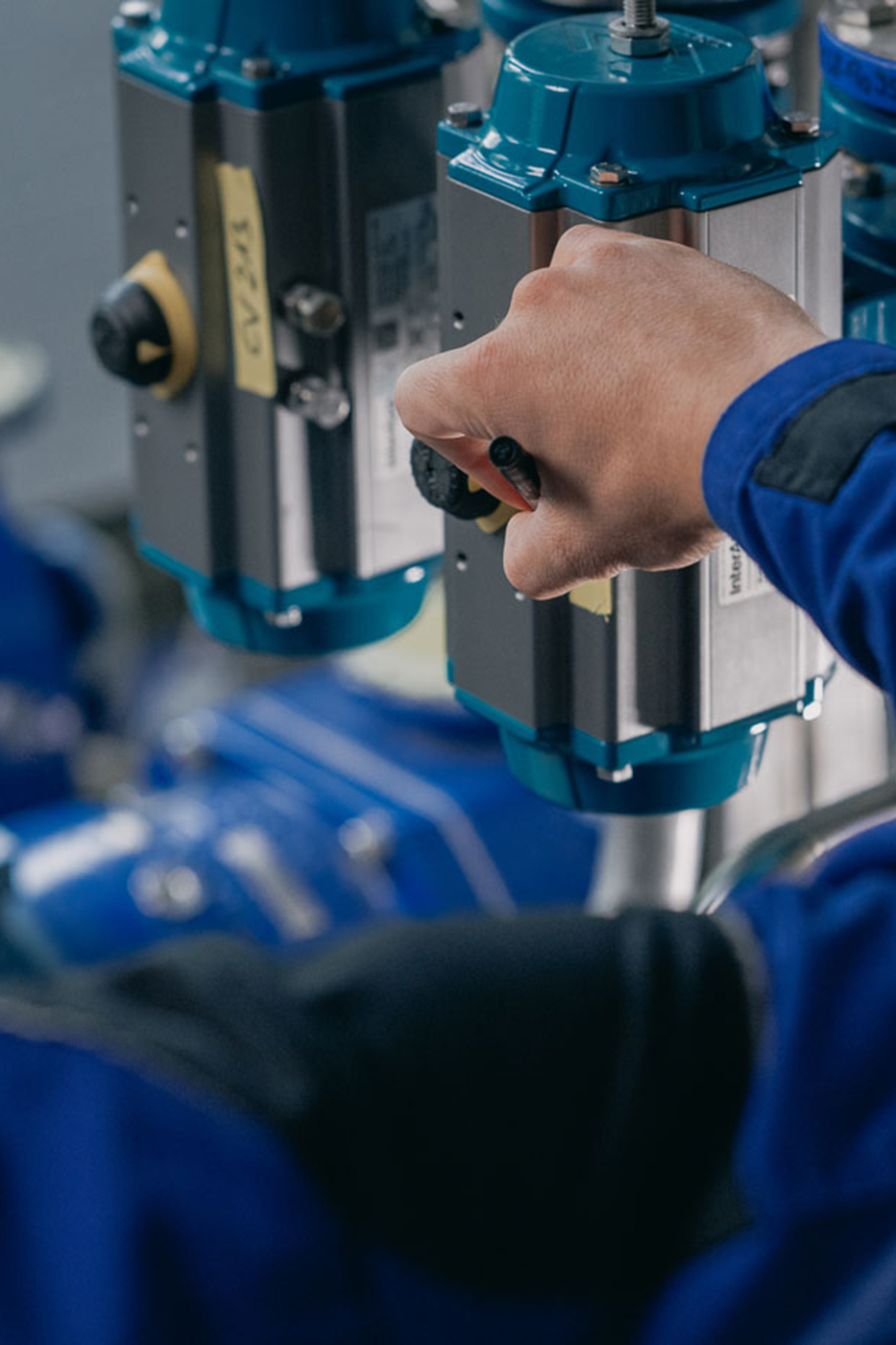
The custom-tailored solution from Penta-Electric
Our solid knowledge and experience with automation projects at Bachem made it possible to develop a quick, custom-fit solution for this plant and carry it out with targeted focus.
The automation was implemented using the M-Pro master project developed by Penta-Electric. Thanks to the structured and standardized architecture of M-Pro, only the basic functions had to be programmed. Most of the software was generated by parametrization.
The benefits for Bachem AG
All of the standards applied by Penta-Electric in planning, programming, installation and qualification enable quick, parallel processing of the tasks mandated, with good reliability in achieving the required functions. The high level of mutual trust between Pent-Electric and Bachem allowed the project to be executed with minimal administrative effort, contributing decisively to the project’s success.
The challenge for Penta-Electric
A large project team had to be staffed within a very short time owing to the short notice prior to project kick-off. Work on planning the EI&C system, generating the functional descriptions and programming the software had to be started in parallel due to the tight project schedule. This parallel processing of multiple tasks required efficient communication. Any changes needed had to be incorporated flexibly and quickly. It was also necessary during installation to closely coordinate with other work packages to keep on schedule.
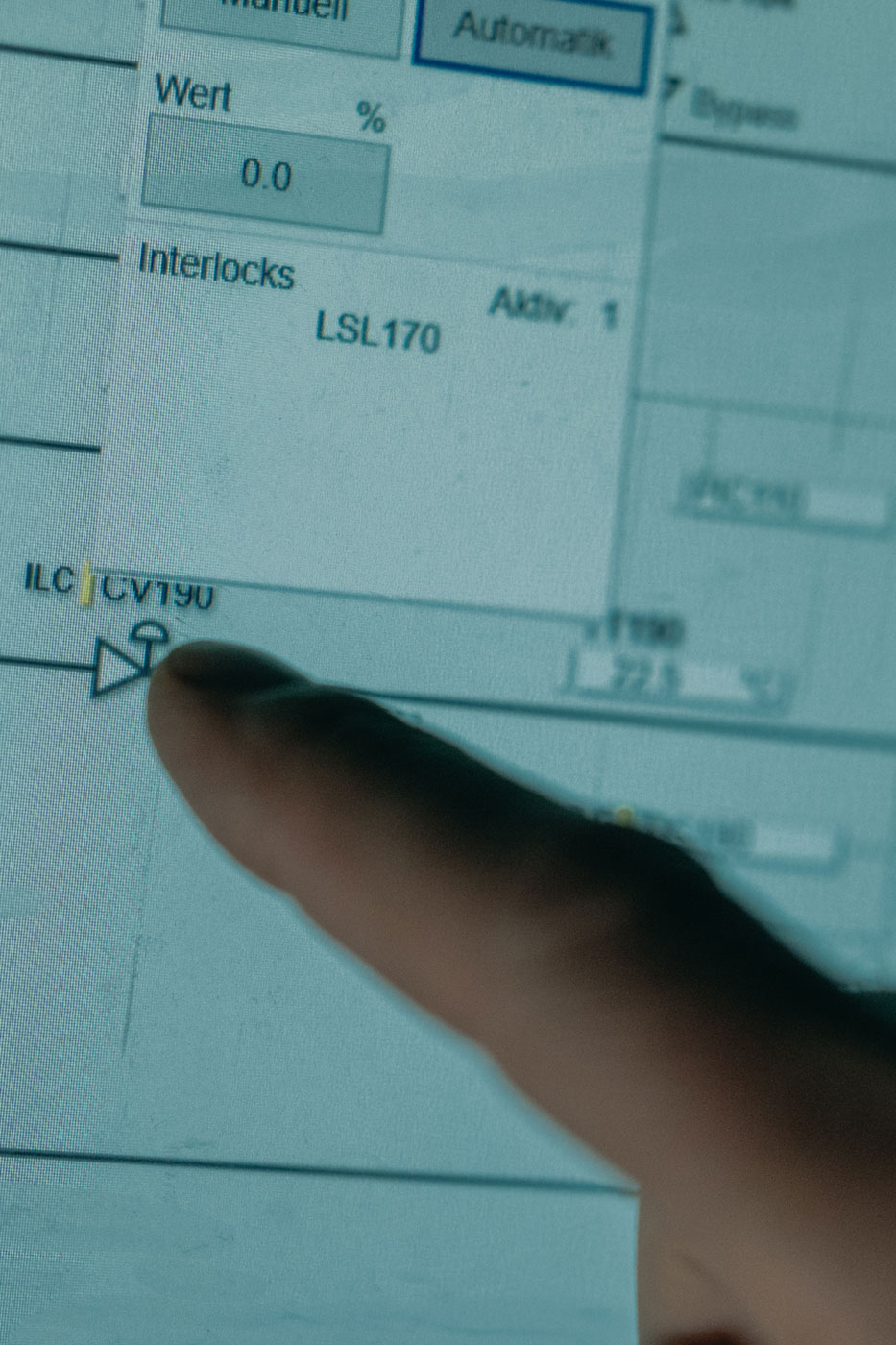
The project in figures
Automation project
Process automation of reactors at Siegfried AG in Zofingen
As one of the leading specialists in industrial automation of process plants, Penta-Electric has comprehensive experience in a wide range of industries – in Switzerland as well as abroad. This includes work for the pharmaceutical industry in particular. We’ll gladly accept any challenge head-on with our extensive expertise and experience, and prove to you that perfection is achievable.
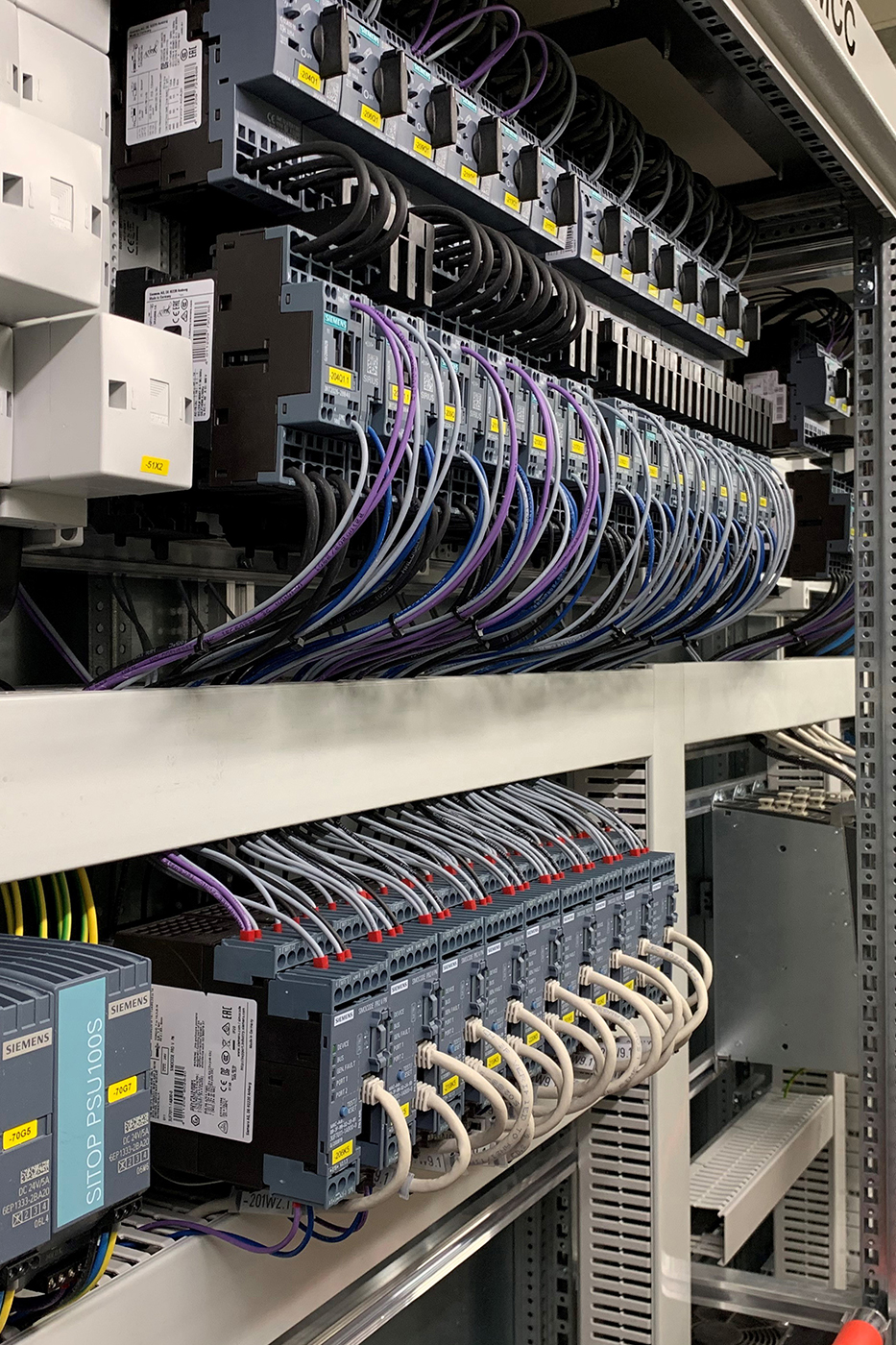
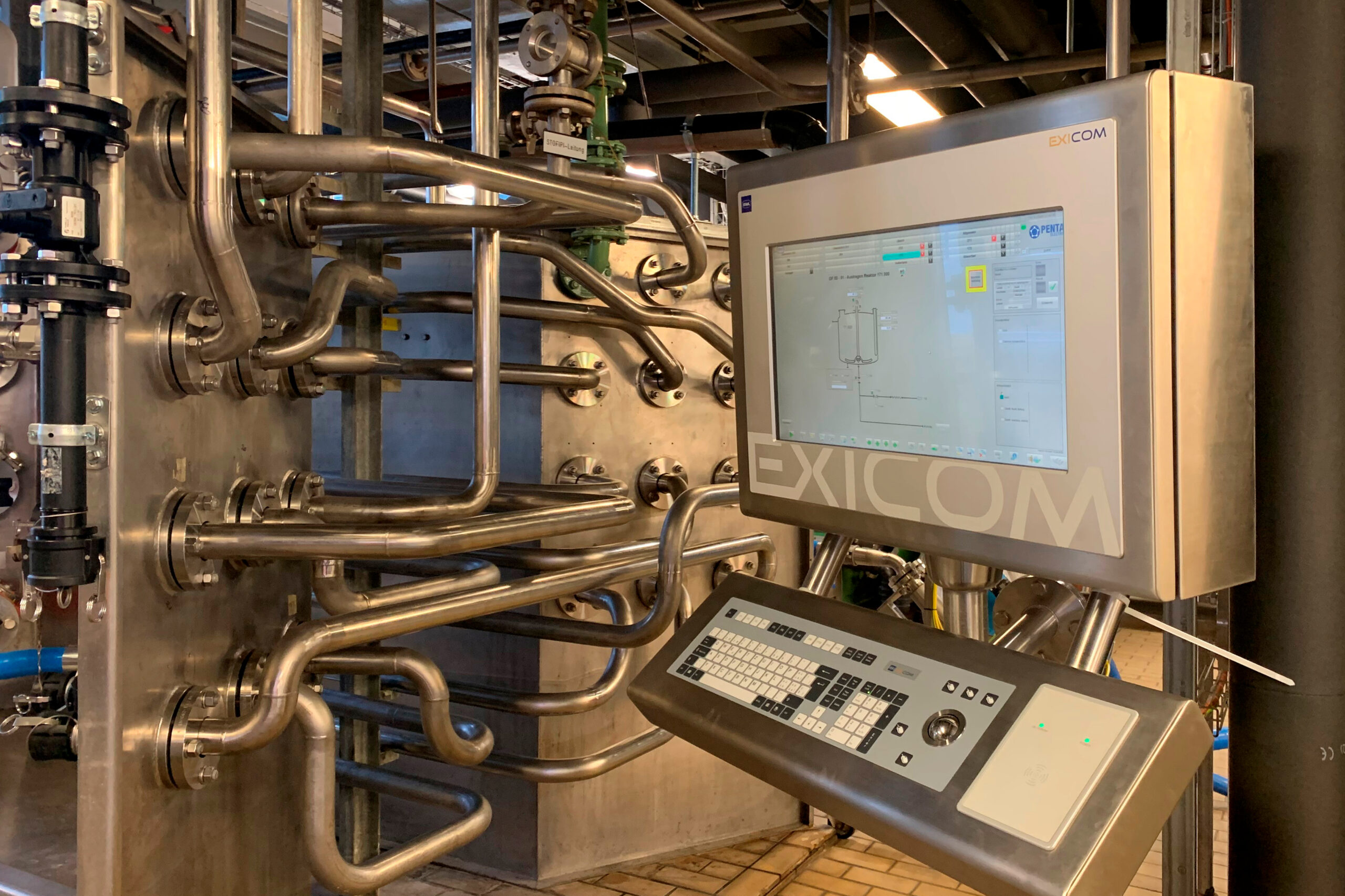
Project description
Siegfried AG introduced new process instrumentation and controls to modernize reactors in its chemical API production. The project had to be executed under extreme time pressure, as production runs had already been scheduled.
The requirements specified by Siegfried AG
The order called for engineering a project with six reactors, five receivers, and seven storage tanks:
- EI&C planning of the complete process automation
- Generating the good manufacturing practice (GMP) documentation in accordance with the Good Automated Manufacturing Practice Guide (GAMP5)
- Programming the PCS7 Control System
- Performing the switchgear cabinet and software factory acceptance testing (FAT)
- Line testing and installation qualification (IQ)
- Functional testing and operational qualification (OQ)
- Providing support for production
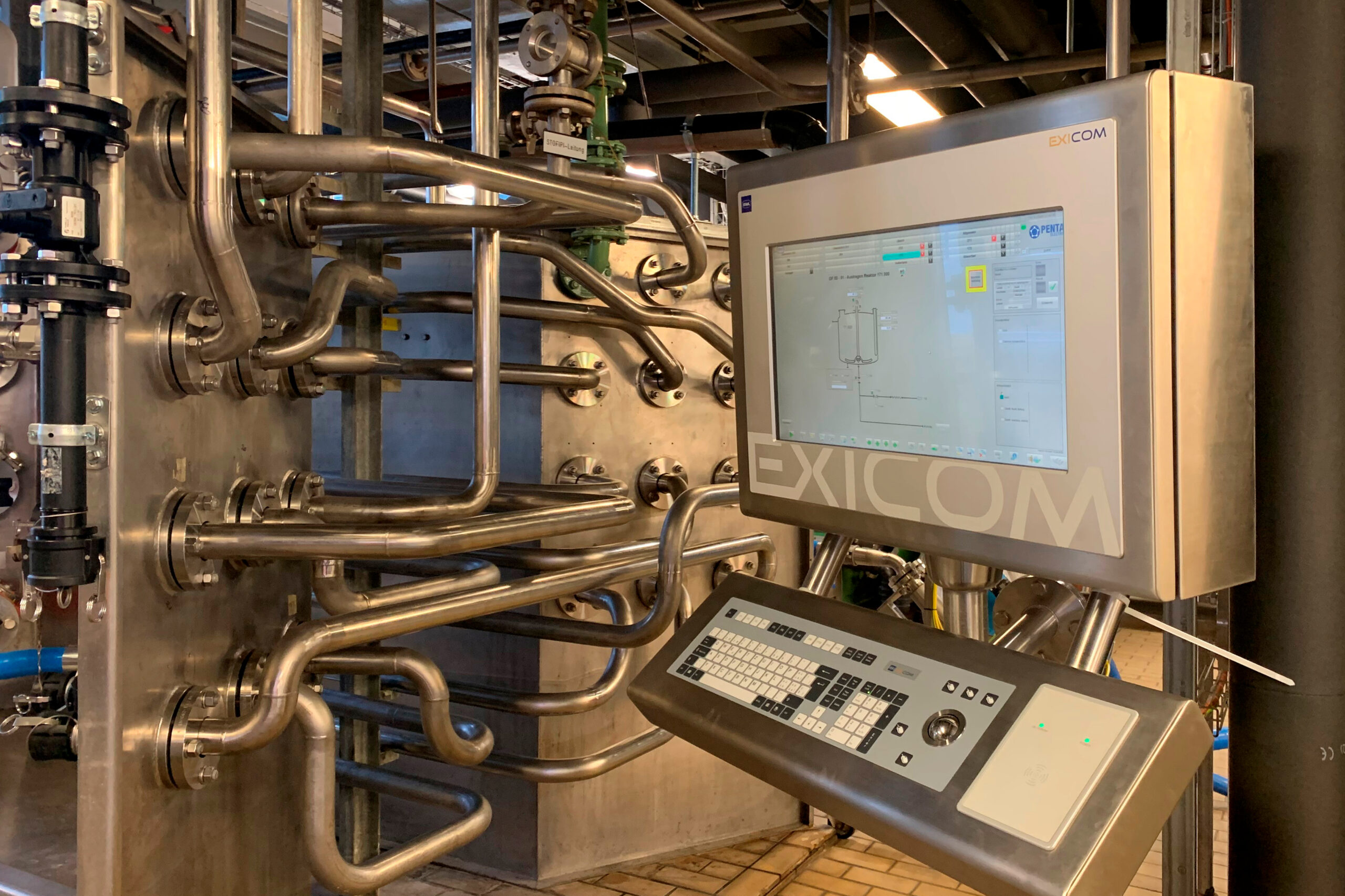
The custom-tailored solution from Penta-Electric
The project was successfully completed to a high standard within a very tight schedule thanks to optimum staffing of the 8-strong team and the close collaboration of everyone involved. Plant operations restarted and have been running continuously 24/7 ever since without a hitch.
The benefits for Siegfried AG
Our vast experience in planning and designing EI&C systems and programming control systems enabled the specified requirements to be successfully implemented within the defined time frame.
The challenge for Penta-Electric
Working under heavy time pressure, personnel had to tackle multiple tasks in parallel while implementing changes flexibly and swiftly. This demanded close, comprehensive communication between all participants.
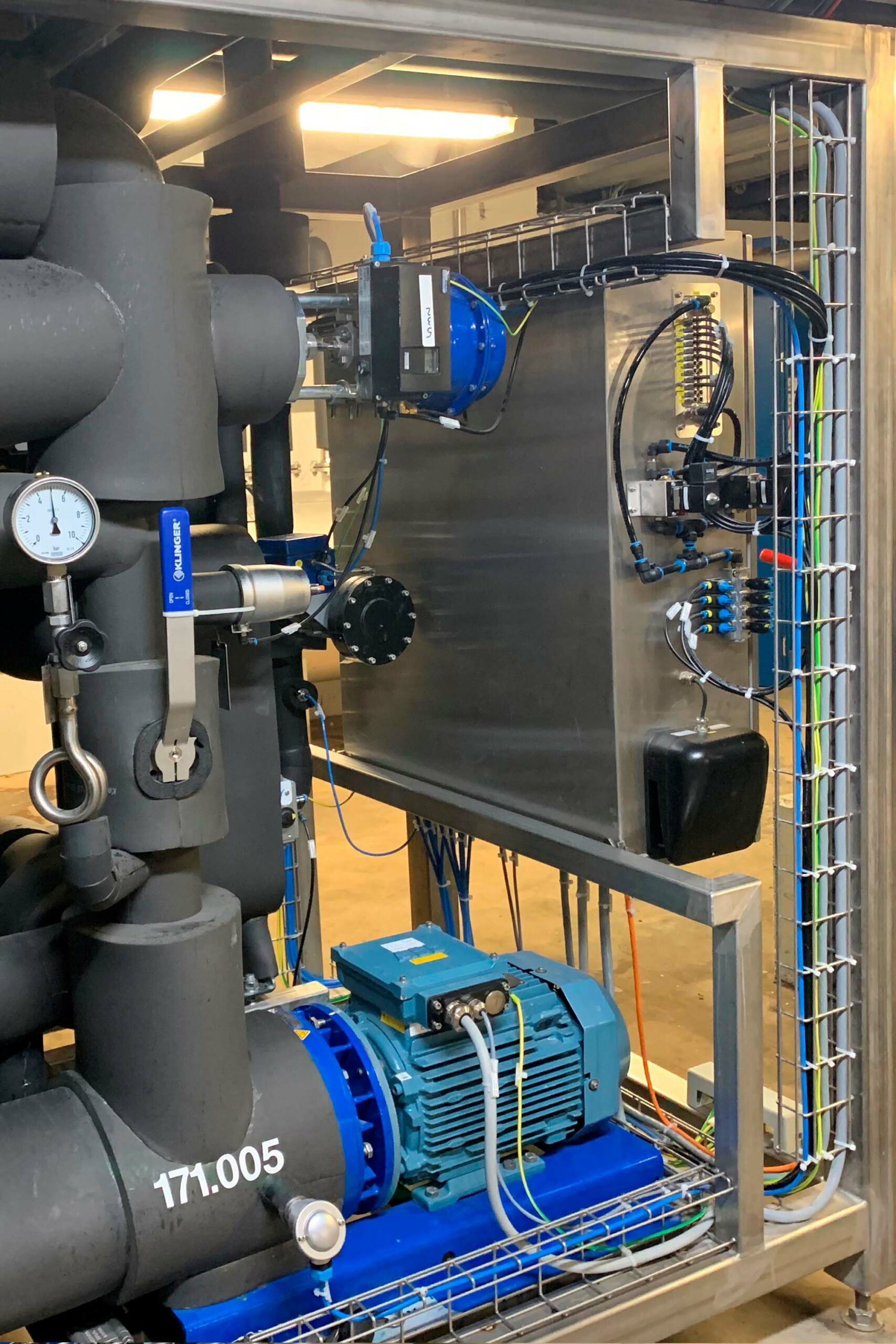